Looking for optimization of your process?
C-QUAND는 플랜트 프로세스를 최적화 할 수있는 민감하면서도 견고하고 운영 및 유지 보수가 용이한 연속 공정 분석기 (continuous process analyzer)입니다. 실리콘 (Z = 14)에서 우라늄 (Z = 92)까지, Total Sulfur 측정, 복합적인 금속 솔루션, PTA 와 PIA 플랜트 및 폐수 스트림과 같은 다양한 응용 분야에서 C-QUAND는 폭넓게 적용됩니다. 업계 최고의 정확도, 재현성, 장기 안정성 및 지속적인 가용성으로 어떠한 공정에서도 신뢰할 수 있는 성능을 제공합니다.
Key benefits
- Continuous multi-element analysis
- Close to no maintenance
- Automated zero and span correction
- Suitable for hazardous and harsh area’s
- Consistent with ASTM and ISO
- 24/7 support through remote access
- Long life SDD and X-Ray tube
“The C-QUAND allows us to have direct and continuous insight in our process, optimizing the use of energy and chemicals”
Our Technology
The non-destructive ED-XRF, X-Ray method has a long-proven track record in the industry for the measurement of elements in liquids. The technology delivers low OPEX costs with high availability (>99.5%). The C-QUAND analyzer offers excellent repeatability with the guarantee of drift-free measurement in the low and high concentration ranges.
The C-QUAND – which has no problematic moving parts – features integrated auto-validation on a solid reference material. The heated sample cell handles more viscous samples and measures at process temperature. Both the sampling system and analyzer wetted parts are available in acid resistant materials. The net effect is a continuous, non-destructive, low maintenance analyzer with calibration intervals of typically more than one year. Considerable savings in analysis time and operational cost – in comparison to alternative analytical techniques – are two of the main benefits of the C-QUAND. It is a robust product fit for harsh process environments and can be fully integrated in process monitoring and control.
X-Ray Fluorescence Principle
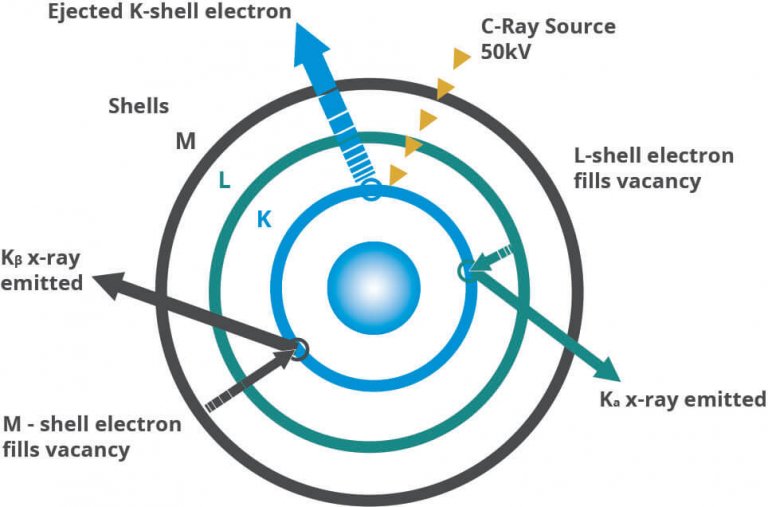
The C-QUAND has a powerful 15 watt, 50 kV X-ray source, with a silver anode. The X-rays displace the inner electron out from the K or L orbit of the atom, leaving a void. The now unstable atom will immidiately fill the void with an electron from the outer orbits. The resulting reduction in energy is emitted as a photon with a specific energy level unique to that particular element. The fluorescence is captured by a silicon drift detector (SDD). It’s count rate being monitored directly proportional to the concentration of the element of interest.
Measuring cell
The X-rays generated by the source are first filtered by one of six different optical filters. The X-rays then travel through a thin window before hitting the actual sample. The window material can be beryllium for sulfur measurement in hydrocarbons, or a polyimide such as Kapton® or Upilex® for the measurement of metals in aqueous solutions.
The measuring cell is constantly flushed with fresh samples. Importantly, this method of measurement is continuous throughout the entire measurement, not just at the beginning. The measuring cell also contains a solid reference metal, which is used for automatic gain correction.
Product Comparison
In the table below, you may find the differences of the two C-QUAND variants available:
Model | C-QUAND-ELT | C-QUAND PLUS |
Technology | ED-XRF | ED-XRF |
Integrated automated flushing system | No | Yes |
Sample Recovery System | Optionally | Optionally |
Typical Applications | Metals refining and recycling, Waste water streams, PTA & PIA plants, and/or other acidic and aqueous samples. | (Ultra) low Sulphur measurement in fuels and/or other highly sensitive (low range) measurements that may be prone to window fouling. |
Certificates
Technical specs
Analytical |
|
Measurement principle | Energy dispersive X-ray fluorescence |
Element range | From Si (Z=14) |
Measurement range | From 0.5 ppm to % levels (application specific) |
Simultaneous elements | Unlimited number of elements per analysis |
Filter wheel | 6 filters |
Accuracy | Appropriate to application |
Calibration | Less than 5 samples |
Central processing and controlling unit |
|
Industrial PC | Linux operating system, custom touch keyboard with 8” TFT color display |
Analog outputs | 2 or 4 x 4-20mA active |
Communications | 4 – 20 mA, MODBUS via RS485 or TCP/IP, Optical Fiber |
Ambient temperature | 5 – 40°C / 41 – 104°F |
Measurement head |
|
X-ray detector | Sillicon drift detector, resolution 135 eV (equals 2.3% at 5.89keV) |
HV power supply | 0-50kV |
Source | 15 W X-ray tube, Ag anode |
Stability | Automatic drift and back scatter peak correction; temperature and ambient pressure correction |
Sample window | Kapton® , Upilex®, beryllium |
Utility requirements |
|
Power supply | 110-230 VAC 50/60 Hz |
Power consumption | 100 VA (150 VA with heated sample cell) |
Instrument air | <4 L/min for Exp. version and required for standard pneumatic valve (electrical actuated valve optional) |
Sample conditions |
|
Sample flow rate | 0,2 – 0.5l/min |
Sample cell temperature | < 80°C / 176°F |
Sample cell pressure | Atmospheric drain |
Viscosity | Less than 100 cSt at cell temperature (Heated sample cell available) |
General |
|
Size | HxWxD = 1000 x 400 x 360 mm / 39,4 x 15,8 x 14,2 inch |
Valve control | Automatic stream switching, automatic cell flushing, automatic validation |
Liquid Sample Recovery Control done by analyser (optional) | |
Inputs | Flow and level alarms (optionally) read by analyser |
Diagnostics | High level of diagnostics |
Remote supervision/control | External control of analyser possible |
Hazardous Area Clasification | ATEX and IECEx Zone 1 (II 2 Ex pxb ICC T4 Gb) |