WIM COMPAS ™는 Wobbe Index, 발열량 (BTU) 및 연소 공기 요구량 지수 (Combustion Air Requirement Index , CARI)를 측정하는 (연료 및 플레어 가스 연소 측정)을 위한 Hobré의 process analyzer입니다. Hobré에서 설계 및 제조 되는 WIM COMPAS ™는 잔류 산소 유형 분석기 (residual oxygen type analyzer)에 대한 20 년 이상의 성공적인 경험을 바탕으로 구축되었습니다. WIM COMPAS ™는 연료 가스 품질 변동으로 인한 저해요소를 최소화하고 연소 과정을 최대의 효율로 끌어 올려, 배기 가스를 최소화하는 방식으로 열 (thermal input)과 공기-연료 비율 (air : fuel ratio)을 제어하는 데 사용됩니다.
Key benefits
- Can be installed outdoors
- Easy to operate
- Unmatched response time
- Suitable for installation in hazardous area
- Safe flameless design
- Handles high dewpoint
- Measures flare gases and sour gases
- Zero Hydrocarbon Emission
“The WIM COMPAS ™ after our flare recovery system is the best way to control we don’t emit any unburned hydrocarbons and monitor compliance at the lowest costs”
WIM COMPAS ™– Versions
-
Cyclic injection
-
Continuous
-
High-temperature
Continuous
This version is designed for top performance where response time, repeatability and reliability count. A small sample flow is mixed continuously with air. The air-fuel mixture undergoes catalytic combustion followed by measurement of the residual oxygen. This provides a direct measure of CARI and correlates to the Wobbe Index as per ASTM 4891-89. By integrating a specific gravity cell, heating value and air demand are also measurable.
Cyclic injection
The WIM COMPAS™ offers an unmatched, robust solution with high availability, for Fuel and flare gas combustion measuring, such as sour gas and flare gas. Hobré has developed an analyzer especially for these kinds of applications, that injects small amounts of gas into an air stream, typically at intervals of 30 seconds. The oxygen peak size is a direct measure of the air demand and proportional to the heating value (BTU).
High-temperature
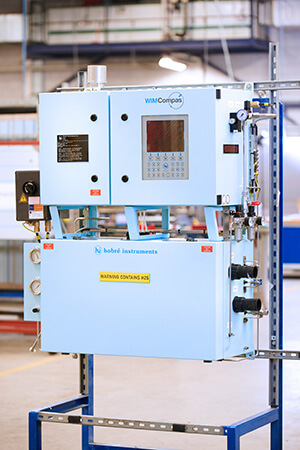
Keeping the gas above dewpoint is crucial to the success of most applications. The WIM Compas™ can be heated up to 55°C (131°F) as standard; high-temperature versions (up to 150°C / 300°F) are available if required
Product Comparison
In the table below, you may find the differences of the WIM variants available:
Model | WIM COMPAS Xpress | WIM COMPAS Flex | WIM COMPAS Pulse | WIM COMPAS Pulse HT |
---|---|---|---|---|
Technology | Residual Oxygen method | Residual Oxygen method | Residual Oxygen method | Residual Oxygen method |
Principle | Continuous type | Continuous type | Injection type | Injection HT |
Typical Response | T90 <5 seconds | T90 <5 seconds | Update time 30 seconds | Update time 30 seconds |
Gas / Application | Natural Gas, LNG – Blending, Turbine (Power) | Fuel gas – Blending, Turbine (Power), Burner/Furnace/Heater/Boiler | Blast Furnace Gas, Coke Oven Gas, Flare gas, Sour gas – Steel applications, Flaring |
Flare gas, Sour gas (high dew point up to 150°C/300°F) – Flaring |
Certificates
Technical Specifications
Application | Natural Gas, Fuel Gas, Flare Gas, Biogas, Blast Furnace Gas, Coke Oven Gas, LNG etc. |
Measuring principle | Residual Oxygen technology |
Sample wetted parts | SS316 |
Installation options | – Safe area |
– ATEX II 2G/3G Ex px [ib] IIC T3/T4 Gb (Zone 1 / 2) | |
– Class 1, Div. 2, Group B, C, D T3 (Zone 2 compliant) | |
– IECEx Ex px [ib] IIC T3/T4 Gb | |
– KCS Ex px [ib] IIC T3/T4 Gb | |
– TRCU (EAC) Ex px [ib] IIC T3/T4 Gb | |
– PECO (CCOE) Ex px [ib] IIC T3/T4 Gb |
MEASURING RANGES (CONTINUOUS VERSION) | |
Wobbe Index | 0 – 100 MJ/Nm3 / 0 – 2500 BTU/scf range (50 MJ/Nm3 / 1250 BTU/scf span)1) |
Accuracy | < ± 0,4% of full scale for Natural Gas |
Repeatability | < ± 0,05% of full scale or ± 30 kJ/Nm3 (whichever is higher) 1) |
Response time | T90 < 5 seconds on Natural Gas |
CARI 2) | 0 – 25 range |
Calorific Value (SG cell option) | 0 – 120 MJ/Nm3 / 0 – 3000 BTU/scf range (50 MJ/Nm3 / 1250 BTU/scf span) 1) |
Response time CV signal | T90 < 5 seconds (typically on Natural Gas) |
MEASURING RANGES (INJECTION VERSION) | |
Calorific value | 0 – 120 MJ/Nm3 / 0 – 3000 BTU/scf range (50 MJ/Nm3 / 1250 BTU/scf span) 1) |
Accuracy | ± 1,0% of full scale |
Repeatability | ± 0,5% of full scale or ± 300 kJ/Nm3 (whichever is higher) |
Update time | Default ~30 seconds (injection interval) |
Air Demand | 0 – 50 range |
Wobbe Index (SG cell option) | 0 – 100 MJ/Nm3 / 0 – 2500 BTU/scf range (50 MJ/Nm3 / 1250 BTU/scf span) 1) |
Update time WI Signal | Default ~30 seconds (Injection interval) |
OUTPUTS (CONTINUOUS/INJECTION) | |
Local HMI | Full color display with capacitive touchpad (all functions) |
Analogue outputs | 2 off isolated 0 / 4 – 20 mA (optionally up to 4), max. 500 Ω load (active) |
Digital outputs | 2 isolated relays (250 VAC) and 8 transistor outputs (24 VDC) standard available (optional: 6ea) |
gital inputs | 8 digital inputs (e.g. start calibration, start validation, etc.) |
Communication options |
– Remote operation / Modbus TCP/IP over Ethernet or Optical fiber |
UTILITIES | Continuous version | Injection version |
Instrument air 3) | 15 Nl/min | 0,2 Nl/min |
50 Nl/min: Ex purge option ATEX / IECEx / Class 1 Div 2 / KCS / TR CU / PESO 4) | 50 Nl/min: Ex purge option ATEX / IECEx / Class 1 Div 2 / KCS / TR CU / PESO 4) | |
Sample flow | ± 1 Nl/min | ± 0.5 Nl/min |
Sample pressure | 1,5 to 5 barg / 21,8 to 72,5 psig | -0.3 to 0.5 barg / -4,4 to 7.2 psig 5) |
Power supply | 115/230 VAC, 50/60 Hz | |
Power consumption | Depending on configuration (typically 1000 W, max. 2500 W) |
INSTALLATION (CONTINUOUS/INJECTION) | |
Mounting | Wall mounting |
Dimensions (HxWxD) | 1000 x 950 x 450 mm (non-Ex version), 1200 x 900 x 450 mm (HT version) |
Weight | 80 kg (non – Ex version), 120 kg (HT version) |
Enclosure protection | Epoxy coated stainless steel (NEMA4, IP65) |
Ambient temperature range | 5 – 40°C / 41°F – 104°F (optional down to -20°C / -4°F and/or up to 55°C / 131°F) |
1) Also available in Kcal/Nm3, kWh/Nm3 etc.
2) CARI= Combustion Air Requirement Index
3) At 4 barg minimum, 10 barg maximum, dry and clean
4) Pre-purge flow: 70 Nl/min
5) Consult factory for diffferent sample pressures
6) Note: Instrument air temperature should not exceed max. ambient temperature
WIM COMPASTM | Xpress4) | Flex | Pulse | Pulse HT | ||
P | Standard | O | O | O | O | |
C | Continuous measurement version (1.5 – 5 barg / 21.3 – 72.5 psig) | O | O | – | – | |
I | Injection version (-0.3 – 0.5 barg / – 4.4 – 7.2 psig) | – | – | O | O | |
115 | Power supply 115 VAC, 50/60 Hz | O | O | O | O | |
230 | Power supply 230 VAC, 50/60 Hz – N/A for Class 1 Div 2 | O | O | O | O | |
0 | No specific gravity meter | O | O | O | O | |
SGU | Hobré specific gravity meter up to 550C / 1300F | O | O | – | – | |
SGC | Oscillation type specific gravity meter up to 800C / 1760F (Hobre standard version) | O | O | O | O | |
SGC HT | Oscillation type specific gravity meter (High Temperature) | – | – | – | O | |
0 | No sample pressure monitoring | O | O | O | O | |
SPM | Sample pressure monitoring | – | O | O | O | |
OFA 1) | Oven Flow alarm | – | O | O | – | |
FPM 1) | Oven flow alarm and Sample pressure monitoring | – | O | O | – | |
0 | Safe area version | O | O | O | O | |
1 | ATEX II 2G Ex Zone 1 IIC T3/T4 Gb (including Power/Signal isolation, excluding Backup purge) | O | O | O | O | |
3 | ATEX II 3G Ex Zone 2 IIC T3/T4 Gb (including Power/Signal isolation, excluding Backup purge) | – | O | O | O | |
Z | CSA Class 1, Div. 2, Group B, C, D T3 version | O | O | O | O | |
E1 | IEC Ex px [ib] IIC T3/T4 Gb (including Power/Signal isolation, excluding Backup purge) | O | O | O | O | |
K | KCS Ex px [ib] IIC T3/T4 Gb (Korea) (including Power/Signal isolation, excluding Backup purge) | – | O | O | O | |
P | PESO/CCOE Ex px [ib] IIC T3/T4 Gb (India) (including Power/Signal isolation, excluding Backup purge) | – | O | O | O | |
T | TRCU/EAC Ex px [ib] IIC T3/T4 Gb (Russia) (including Power/Signal isolation, excluding Backup purge) | – | O | O | O | |
2 | 2 analog outputs | – | O | O | O | |
4 | 4 analog outputs | Included | O | O | O | |
0 | No serial communication | – | O | O | O | |
R | Remote operation / Modbus TCP/IP over Ethernet | – | O | O | O | |
RO | Remote operation / Modbus TCP/IP over Optical fiber | – | O | O | O | |
M | Modbus RTU over RS485 | – | O | O | O | |
MO | Modbus RTU over Optical fiber | – | O | O | O | |
RM | Remote operation / Modbus TCP/IP over Ethernet and Modbus RTU over RS485 | Included | O | O | O | |
RMO | Remote operation / Modbus TCP/IP and Modbus RTU over Optical fiber | – | O | O | O | |
0 | No extra isolated relays (standard 2 off isolated relays) | O | O | O | O | |
R | 8 off isolated relays | – | O | O | O | |
0 | No fastloop inside the analyzer | O | O | O | O | |
F | Fastloop installed inside analyzer | O | O | O | O | |
FA 1) | Fastloop with alarm installed inside analyzer | – | O | O | – | |
0 | Standard ambient temperature range (5 – 40°C / 41 – 104°F) | O | O | O | O | |
H | Heated electronics for low ambient temperature (down to -20°C / -4°F) | O | O | O | O | |
C | Cooler for high ambient temperature (up to 55°C / 131°F) | O | O | O | O | |
HC | Version for ambient temperature range (-20 – 55°C / -4 – 131°F) | O | O | O | O | |
1 | Analyzer suitable for wall mounting | O | O | O | O | |
HT | High Temperature application (max. 150°C / 300°F) | – | – | – | O | |
ZE 2) | Zero HC Emission (max. backpressure 0.5 barg / 7.2 psig) | O | O | – | – | |
FEH2 3) | Frontal Elution H2 (Hydrogen measurement) | – | – | – | O |
Notes:
1) The standard Flow alarm cannot be used in the High Temperature application. Please consult Hobré if required.
2) The Injection version is suitable for Zero HC emission operation by design.
3) The HC (Heater/Cooler) option is mandatory in case of the Pulse HT analyzer in combination with FEH2 Hydrogen measurement.
4) The Xpress model is suitable for Natural gas / LNG application only.
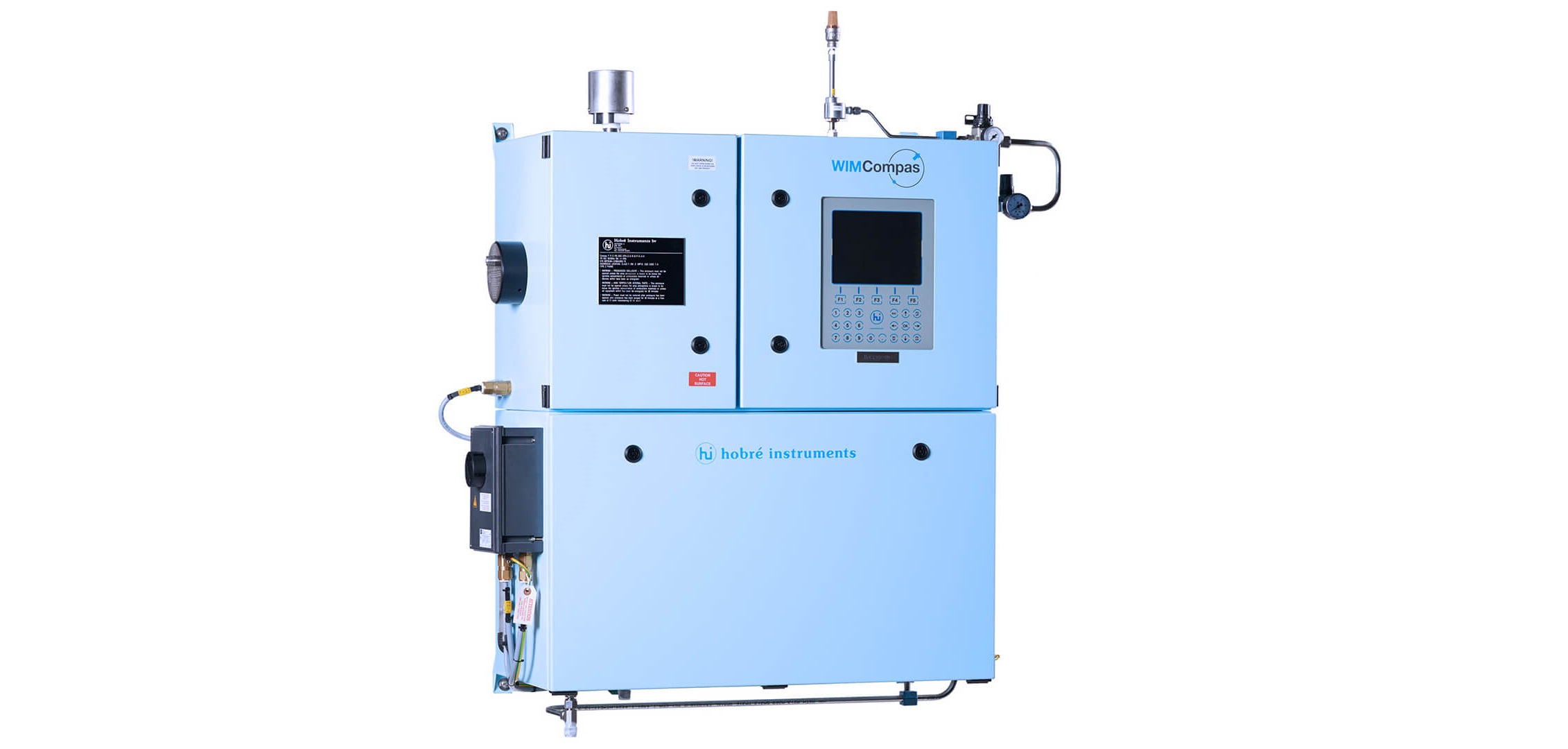
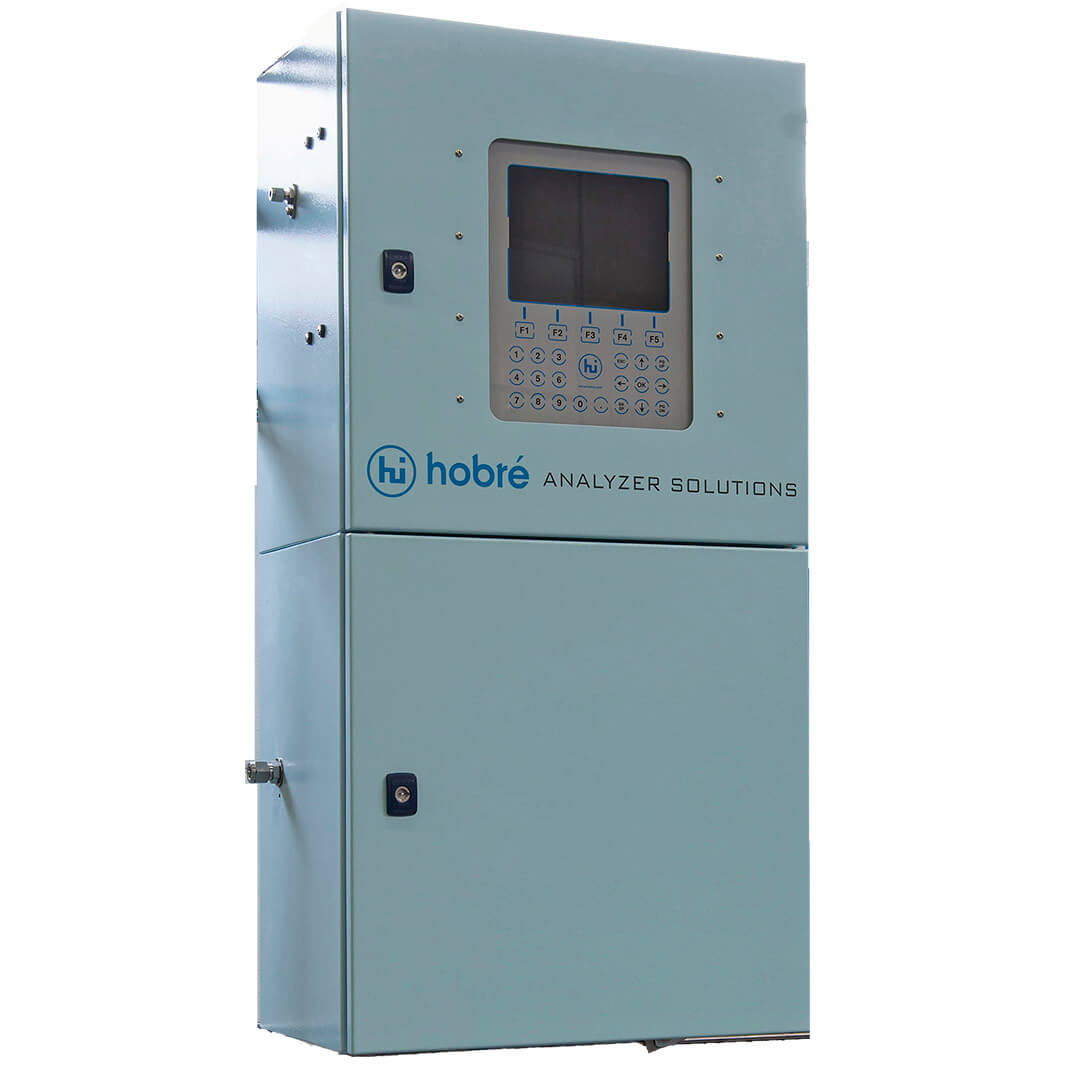
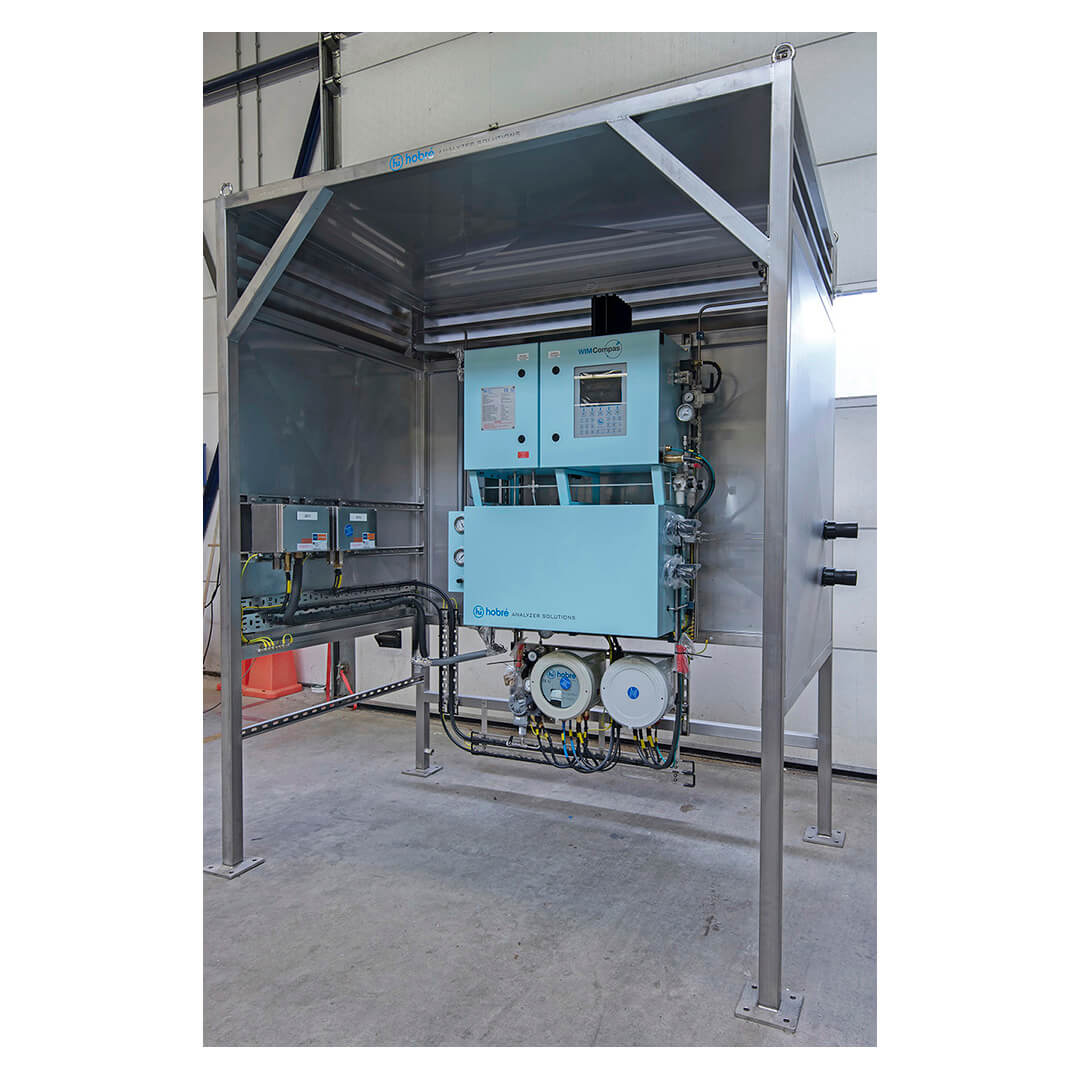
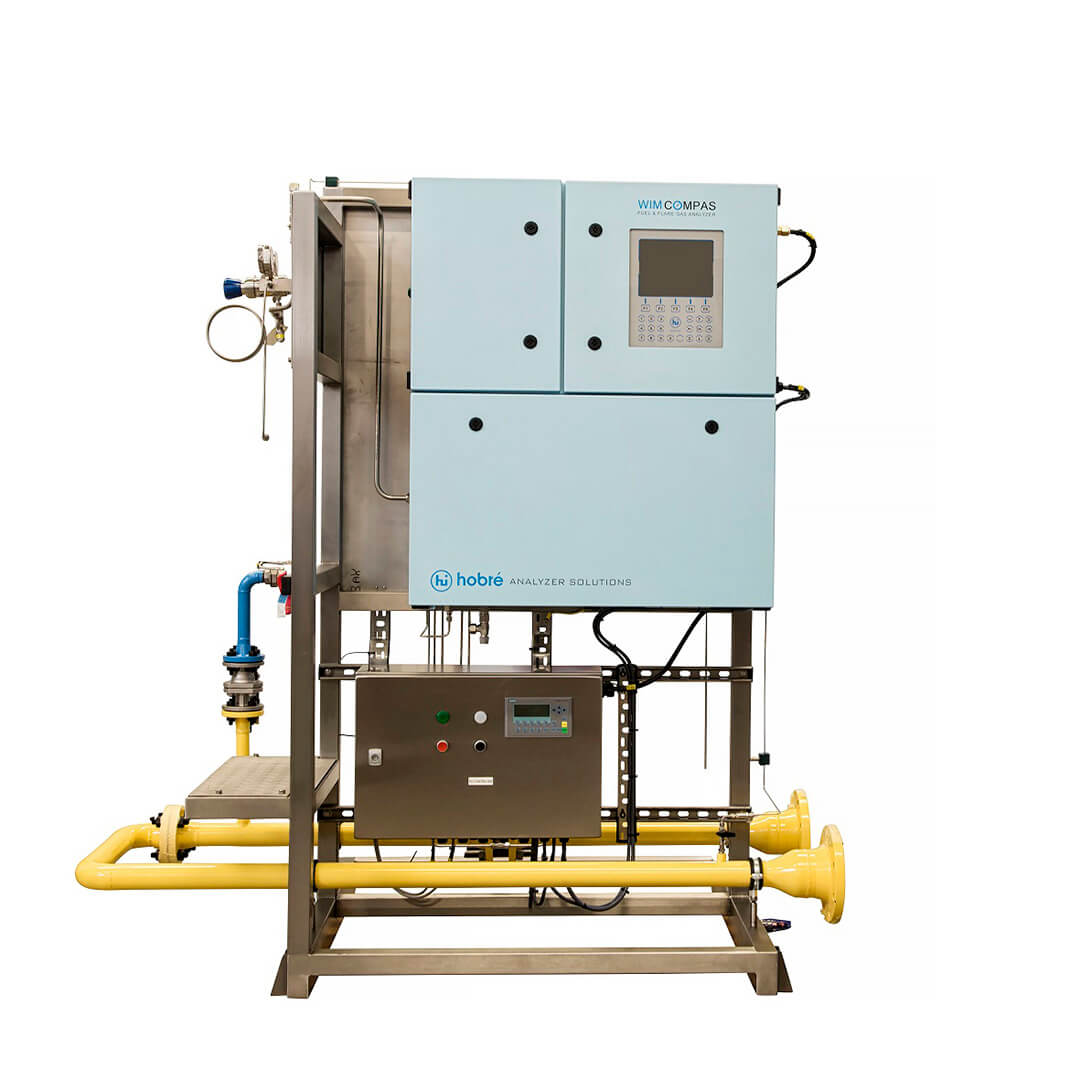
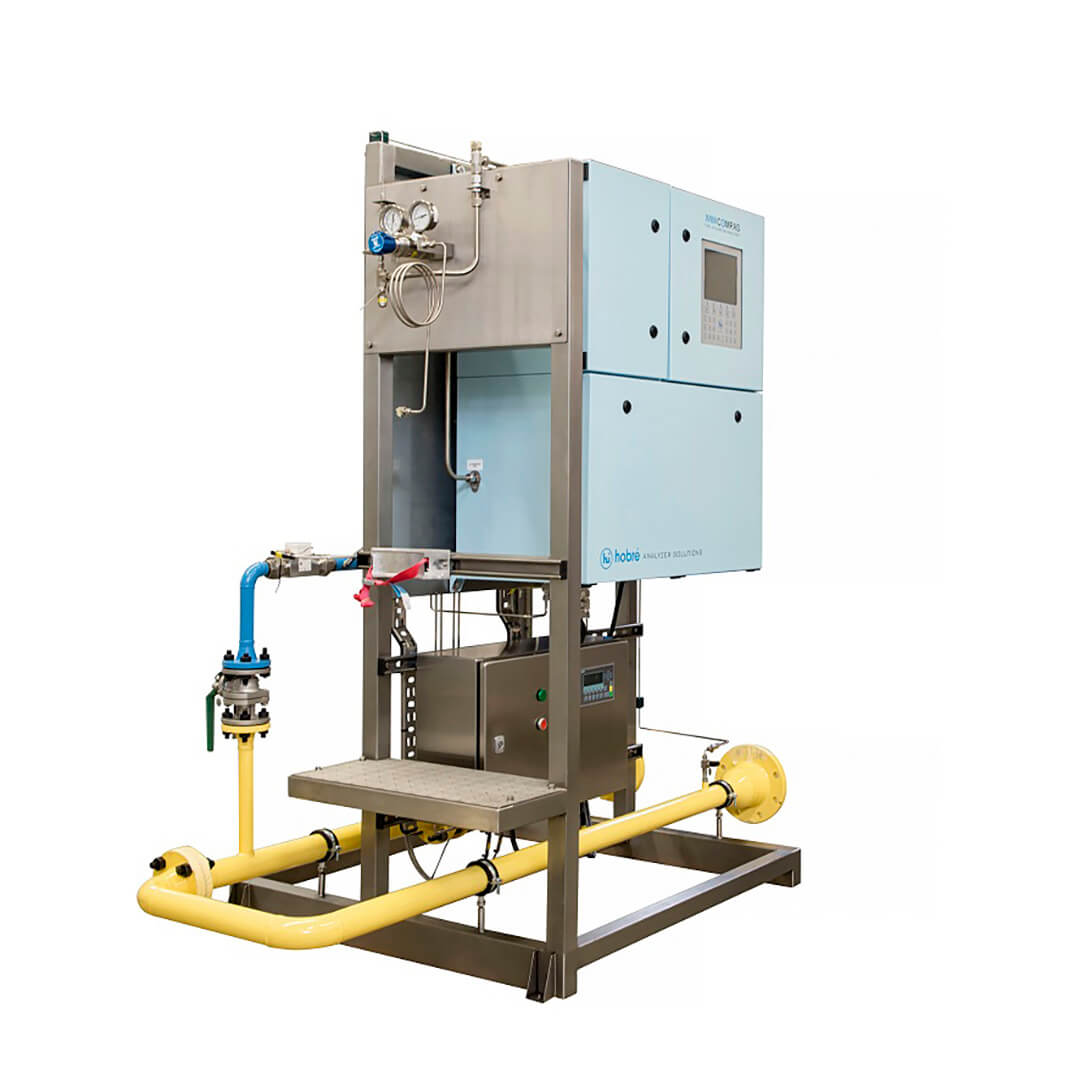