Understanding composite and thermoset cure
새로운 열 경화제나 복합제의 경화 과정은 근본적으로 알려져 있지 않습니다. 예를 들어 해당 재료가 가열되면 어떻게 될 것이고, 압력을 가하기 가장 좋은 시점은 언제이며, 다른 온도에서 얼마나 빠르게 반응할 것인가와 같은 질문에 관한 것입니다. Dielectric cure monitor 또는 Dielectric analyzer (DEA)는 실험실과 제조 환경 사이의 격차를 좁히기 위한 DSC와 DMA보다 전통적인 열 분석 기법 중 하나입니다.
DEA, DSC 및 DMA는 다양한 재료 특성을 측정합니다. 본 유전율 분석기는 DSC나 DMA를 대체할 수는 없으나 보완할 수 있습니다. R&D 및 공정 개발에서 매우 간단한 시료 준비와 모든 시점의 경화 거동을 분석할 수 있는 장점이 있습니다. DSC 또는 DMA 측정을 미루어도 본 기기와 함께 연구 개발을 가속할 수 있습니다.
Characteristics of thermoset cure
Dielectric cure monitoring measures a polymer’s resistivity (ρ) and permittivity (ε’), which are dielectric properties. In general resistivity provides the most useful information about cure state. More specifically, before gelation the change in frequency independent resistivity (ρDC), due to the flow of mobile ions, is often proportional to the change in mechanical viscosity. To emphasize this relationship, the term ion viscosity (IV) was coined as a synonym for frequency independent resistivity.
A thermoset cures when monomers react to form polymer chains then a crosslinked network. The reaction is usually exothermic—generating heat—and may additionally be driven by the heat of a press or oven. A plot of log(ion viscosity) is a simple way to characterize the progress of cure and Figure 2-1 shows the behavior of a typical thermoset with one ramp and hold step in temperature.
At first as temperature increases, the material softens or melts and mechanical viscosity decreases. Mobile ions also experience less resistance to movement and ion viscosity decreases. At this point the reaction is still slow. As the material becomes hotter, the cure rate increases.
At some time the accelerating reaction begins to dominate; mechanical viscosity reaches a minimum then the material becomes more viscous. Electrically, the increase in ion viscosity due to polymerization overcomes the decrease in ion viscosity due to higher temperature. Ion viscosity also reaches a minimum then increases due to chain extension, which presents a greater and greater impediment to the flow of ions. The gel point is the beginning of infinite network formation or crosslinking.
At gelation mechanical viscosity rapidly increases until it becomes infinite. Although viscosity becomes immeasurable at the gel point, the change in ion viscosity continues to provide useful information and after gelation is often proportional to the change in modulus. As a result, DEA can follow material state throughout cure.
Typical ion viscosity behavior of thermoset cure during thermal ramp and hold
As cure progresses, ion viscosity increases continuously until the concentration of unreacted monomers diminishes and the reaction rate decreases. Consequently, the slope of ion viscosity also decreases and eventually reaches a value of zero when cure has stopped completely.
Differential scanning calorimetry
Differential scanning calorimetry, one method for studying polymers, measures glass transition temperature Tg, which changes with cure state. For a particular epoxy, Figure 2-2 shows Tg measured with DSC and compared with results from dielectric cure monitoring.
Each DSC data point requires curing the material to a chosen time, quenching the sample to stop cure and then performing the DSC analysis. This test must be repeated at multiple points during processing to obtain enough data to see the cure curve—a very tedious and repetitive task. In contrast, the cure curve from dielectric cure monitoring was obtained from a single test.
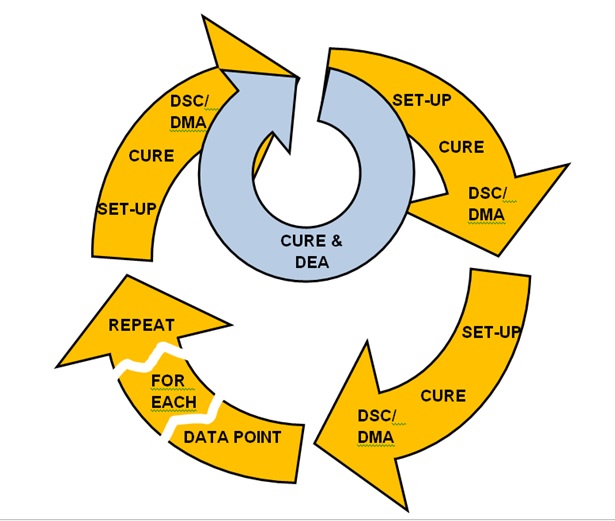
본 제품은 실험실, QA/QC bench 또는 제조실과 같은 매우 다양한 조건에서 실험이 가능한 장점을 가지고 있습니다. 다른 복합적인 경화 거동 분석기에는 이러한 다기능성이 없습니다. 본 분석기는 오븐, 핫플레이트, 프레스, 몰드, 오토클레이브 또는 개발 또는 제작 중인 요소에도 적용이 가능합니다. 본 측정기는 소규모 또는 대규모의 재료에 내장되어 경화 속도와 경화에 따른 발열의 영향을 직접적으로 측정합니다.
본 유전율 측정기는 DSC 또는 DMA와 같이 일반적인 실험 및 측정과 관계가 있습니다. 이에 따라 본 기기는 연구소에서 제조 시설, 제조 시설에서 제품 품질 책임자에게 종합적인 경화 거동에 대한 정보를 제공하는 "매개" 역할을 할 수 있습니다.
When working on a new thermoset or composite, the cure process is essentially unknown. What happens when the material is heated? When is the best time to apply pressure? How fast does the material react at different temperatures? Dielectric cure monitoring, or dielectric analysis (DEA) takes its place among more conventional thermal analysis techniques of differential scanning calorimetry (DSC) and dynamic mechanical analysis (DMA) to bridge the gap between laboratory and manufacturing environments.
DEA, DSC and DMA measure different material properties. DEA does not replace either DSC or DMA, but instead complements them. In R&D or process development, DEA has the advantage of very simple sample preparation and the ability to make measurements during the entire cure in real time. Dielectric cure monitoring can accelerate R&D by deferring the need to make laborious DSC or DMA tests until near end of development.
DEA has the advantage of allowing material tests in a wide variety of conditions, both in the laboratory, the QA/QC bench or the manufacturing floor. No other method of composite cure monitoring has this versatility. Dielectric cure monitoring may be performed in an oven, on a hot plate, in a press or mold, in an autoclave or in an actual composite part being developed or manufactured. When embedded in a part or a large mass of material, the dielectric sensor can directly measure the effect of an exotherm on the rate of composite cure.
Dielectric cure monitoring correlates with measurements from more conventional laboratory tests, such as differential scanning calorimetry or dynamic mechanical analysis. As a result, DEA can act as the “go between” that brings information from the research lab to the manufacturing floor, and from the manufacturing floor to the manager responsible for product quality.
Reference :
Lambient TechnologiesTM Technical Overview 3.02—Dielectric Cure Monitoring Applications, Page 5
상세한 사항은 아래 첨부된 자료를 참고 부탁 드립니다.
하기