플라스틱 정성분석, 품질분석, 비교분석기 (IdentiPol)
플라스틱 유전율측정기 (DEA, Dielectric analyzer)
인장, 압축, 굴곡강도, 점착력측정기 (TXA 재료물성분석기, UTM 만능재료시험기)
유리전이, 용융점, 용융열, 결정화온도, 산화도입기 (OIT) 측정기 - DSC 시차주사열량계
점탄성측정기 (Storage Modulus, Loss Modulus, Tangent Delta) - DMA Dynamic Mechanical Analyzer
Microscope Hot / Cold Stages
Energy Dispersive X-Ray Fluorescence Spectrometer for RoHS
- AL-NP-5010A는 기본적으로 RoHS 테스트 용으로 설계 되어, 샘플 내 독성이 있는 원소 유해한 원소 (Pb, Br, Hg, Cr, Pb)를 테스트하는 데 추천됩니다. 본 모델은 검량선을 작성하지 않아도 되는 모델입니다.
Laser Micromachining Systems 고분자 재료 미세가공 시스템
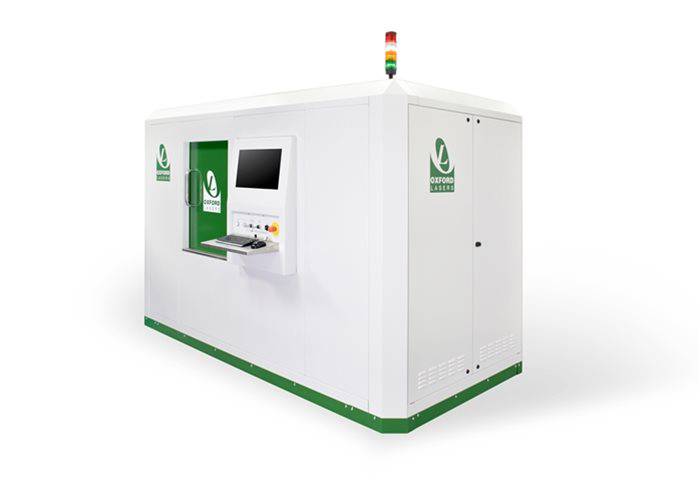
A wide range of polymers can be laser machined with extremely high precision. This includes polymers that occur in both the synthetic and natural form.
- Many polymers can be laser drilled and cut with extreme quality and precision, but care needs to be taken with the judicious choice of laser wavelength and pulse length to ensure best quality results. Laser drilled micro holes can be created as small as a few microns, whereas laser micro cutting can cost effectively produce features up to several centimetres and beyond.
To ensure the highest precision while processing both polymers and engineering plastics, the correct choice of processing conditions is extremely important to ensure that cumulative heat effects are avoided and high-quality results at the micron level are achieved. Often the colour of the polymer can significantly influence the choice of processing conditions.
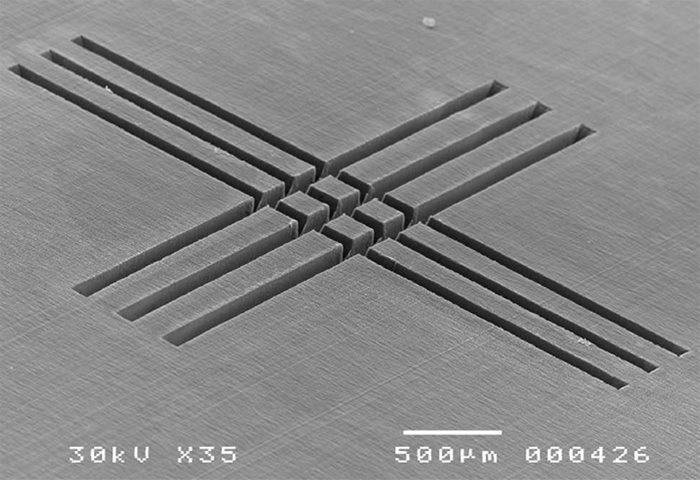
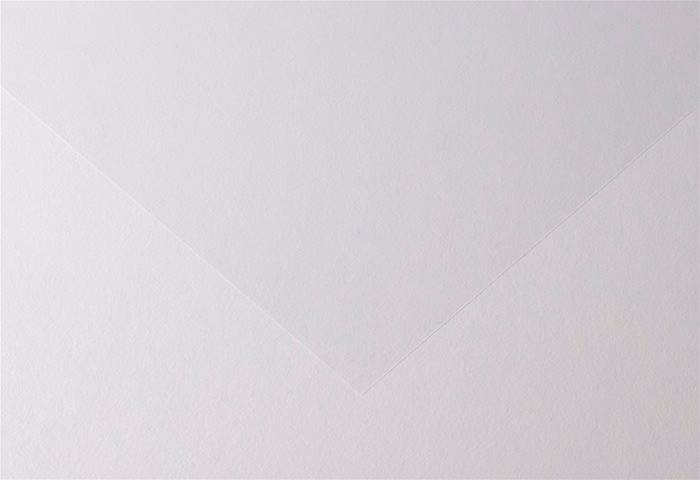
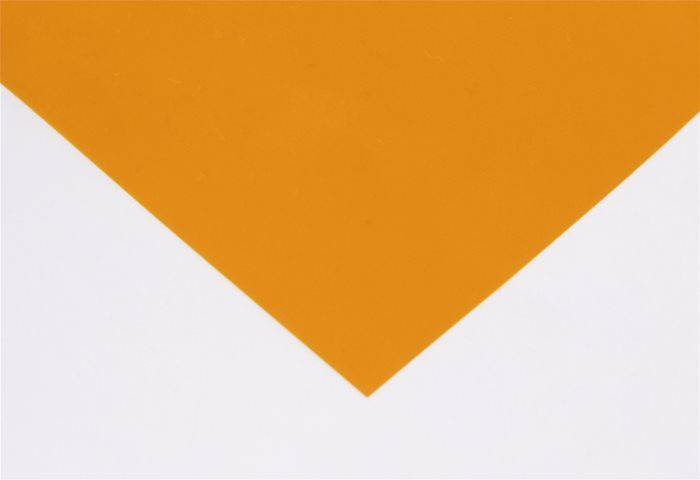
Polymers as thin as a few tens of microns through to thicknesses of several millimetres can be drilled and cut.
A sample of polymers we can machine include:
- ABS | Acrylics | Flouropolymers (PTFE/Teflon/FEP etc) | Polyimides (inc. Kapton) | Plus many more...
Universal Testing Machine (UTM) from Testresources, USA
- Plastics are synthetic or semi synthetic viscoelastic materials composed of organic polymers and organic or synthetic additives. The behavior of plastics under stress depends on the length of time they are exposed to the stress and the temperature the exposure occurs. The applications for plastic materials are broad because the mechanical properties of plastics are defined by their molecular makeup which may be customized to meet the requirements of the desired application. The more common forms of plastics and their applications are styrene foam or Styrofoam which is used as insulation and packaging, PVC which is used in plumbing and nylon which is a flexible yet strong material used in the clothing industry.
Plastic Material Testing Goal:
Testing a plastic’s mechanical properties determines if it will meet the requirements of the desired application. Plastics are similar to metals in that they can be manufactured or produced using a wide range of procedures and material components in order to achieve the desired material characteristics. Typically the desired characteristics of plastic products are low cost, low weight, high toughness, high elasticity and ductility, and high strength in tension, compression, flexure, torsion and shear. These properties are defined by the chemical makeup of the material components used to produce the plastic and are more specifically dependent upon their molecular weight, hardness, density, and resistance to heat and solvents.
Common Plastic Test Methods:
Depending upon the expected stresses and loads of the application any number of tests will be performed upon a plastic material to predict its behavior under those forces. The most common tests of plastics are tensile tests, compressive tests, flexure tests, shear tests and torsion tests. Tension and compression tests involve the loading of the plastic along its longitudinal axis, but where tension tests pull the ends away from each other compression tests push them together. Shear testing can be similar to tension and compression tests but the key difference is in the offsetting of the ends of the test sample so that when the load is applied the outer surfaces of the sample move in opposing direction causing the sample to fail in a sliding motion. Flexure tests require the load to be applied to the midsection of the test sample so that it is bent into a “U” or “V” shape with the outside surface experiencing tensile forces and the inside face experiencing compressive forces. Torsion testing simply requires a rotational force or torque to be applied to one end of the sample while the other end is anchored. All of these tests are run until the sample breaks or ruptures with the stress and strain values recorded throughout the duration.
Plastic Testing Specimens:
There are four common methods for producing plastic test specimens: machining, die-cutting, injection molding and compression molding. Machining test specimens is achieved by taking a straight sample of the test material and shaping it into the desired shape by grinding or cutting away the undesired material and is usually done for more rigid plastics that may be subject to the formation of defects is created using one of the other processes. Die cut test samples are fairly easy to produce as many samples can be cut from a single sheet of material almost like a cookie cutter cutting cookies from a piece of dough. Injection molded specimens are produced by heating the plastic material until it is a liquid and injecting it into the mold of the desired shape, which allows for the production of highly specialized shapes. Specimens that are compression molded are formed by pushing the material into a mold so that is deformed into the shape of the mold. Choosing which process to use depends entirely upon the characteristics of the material that the test is performed upon.
Related Articles
- Plastic Pipe and Pipe Welds Testing
- Gasket Materials Compression Test Equipment
- Torsion Test Equipment for Plastics
- Tensile Testing Machines for Plastics, Polymers & Composites
- Tensile Testing of Plastics & Composites | Equipment for ASTM D638
- Tensile Testing of Plastic Thin Film | Equipment for ASTM D882
- How to Configure Equipment for Tensile Testing Plastic and Polymer Materials
- Charpy Impact Strength of Plastics | Testing Equipment
- Izod Impact Strength of Plastics | Testing Equipment
- Fracture Toughness Test Equipment for Plastics
- Bond Strength Testing of Plastics
- Plastic Composite Compression Testing Accessories
- Three Steps for Compression Testing Plastic
- Metal Electroplated Plastics Testing
- Plastics Coefficient of Friction (COF) Testing
- Thermoplastic & Thermoset Plastics Tensile Testing
- Polyethylene HDPE MDPE LDPE Plastics | Tensile & Flexural Tests
- Plastics Compression Testing
- Injection, Extrusion, & Compression Molded Plastic Material Testing
- Fiberglass Strength Testing | GRP & GFRP Material Properties
- PVC Polyvinyl Chloride Materials Testing
- Plastics & Composites Tensile Test | ASTM D638 ISO 527
- Plastic Sheet Thin Film Tensile Test | Equipment for ASTM D882
- 180 Degree Peel Testing for Plastic Film
- In-Plane Shear Testing for Reinforced Plastics
- Three Point Flexural Bend Test Fixture for Plastics
- Flexural Test of Plastics & Composites using Three and Four Point Bend Fixtures
- How to define test equipment requirements for flexural properties of plastics
Applicable Standards
- ASTM D256 Izod Impact Resistance of Plastics
- ASTM D6110 Charpy Impact Resistance of Notched Specimens of Plastics
- ASTM D624 Tear Testing for Rubber and Elastomers
- ASTM D6272 Four Point Flexural Bend Test Machine for Plastics and Insulating Materials
- ASTM D638 Tension Testing for Plastics
- ASTM D695 Compression Testing for Rigid Plastics
- ASTM D7774 Flexural Fatigue Test Equipment for Plastics
- ASTM D790 Testing for Flexural Properties of Plastics and Insulating Materials
- ASTM D882 Tensile Testing for Thin Plastic Sheeting
- ISO 13802 Pendulum Impact Test of Plastics | Machines
- ISO 179 Charpy Impact Strength of Notched Plastics | Testing Equipment
- ISO 180 Izod Impact Strength of Plastic | Test Equipment
- ISO 527 - Tensile Test of Plastics Composites
하기